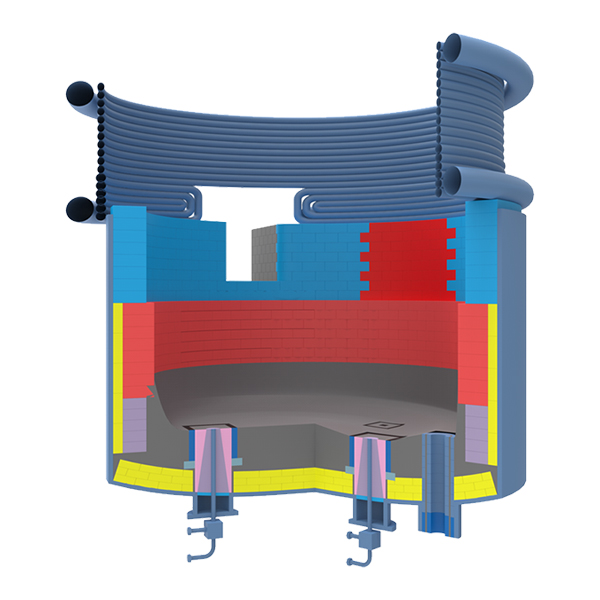
I requisiti generali per i materiali refrattari per forni ad arco elettrico sono:
(1) La refrattarietà deve essere elevata. La temperatura dell'arco supera i 4000 °C e la temperatura di fabbricazione dell'acciaio è compresa tra 1500 e 1750 °C, a volte fino a 2000 °C, pertanto i materiali refrattari devono avere un'elevata refrattarietà.
(2) La temperatura di rammollimento sotto carico deve essere elevata. Il forno elettrico funziona in condizioni di carico ad alta temperatura e il corpo del forno deve resistere all'erosione dell'acciaio fuso, quindi il materiale refrattario deve avere un'elevata temperatura di rammollimento sotto carico.
(3) La resistenza alla compressione deve essere elevata. Il rivestimento del forno elettrico è influenzato dall'impatto della carica durante il caricamento, dalla pressione statica dell'acciaio fuso durante la fusione, dall'erosione del flusso di acciaio durante la spillatura e dalle vibrazioni meccaniche durante il funzionamento. Pertanto, è necessario che il materiale refrattario abbia un'elevata resistenza alla compressione.
(4) La conduttività termica deve essere bassa. Per ridurre la perdita di calore del forno elettrico e il consumo energetico, è necessario che il materiale refrattario abbia una scarsa conduttività termica, ovvero il coefficiente di conduttività termica deve essere basso.
(5) La stabilità termica deve essere buona. Nel giro di pochi minuti dalla spillatura alla carica nella produzione di acciaio in forno elettrico, la temperatura scende bruscamente da circa 1600 °C a meno di 900 °C, pertanto i materiali refrattari devono avere una buona stabilità termica.
(6) Elevata resistenza alla corrosione. Durante il processo di fabbricazione dell'acciaio, le scorie, i gas di forno e l'acciaio fuso hanno tutti forti effetti di erosione chimica sui materiali refrattari, pertanto è necessario che i materiali refrattari abbiano una buona resistenza alla corrosione.
Selezione dei materiali refrattari per le pareti laterali
I mattoni MgO-C vengono solitamente utilizzati per costruire le pareti laterali dei forni elettrici privi di pareti di raffreddamento ad acqua. I punti caldi e le linee di scoria sono sottoposti alle condizioni di servizio più severe. Non solo sono gravemente corrosi ed erosi dall'acciaio fuso e dalle scorie, ma subiscono anche gravi danni meccanici dovuti all'aggiunta di rottami, e sono anche soggetti alle radiazioni termiche dell'arco. Pertanto, queste parti sono realizzate con mattoni MgO-C dalle prestazioni eccellenti.
Per le pareti laterali dei forni elettrici con pareti raffreddate ad acqua, grazie all'impiego della tecnologia di raffreddamento ad acqua, il carico termico aumenta e le condizioni d'uso sono più rigorose. Pertanto, è opportuno scegliere mattoni MgO-C con buona resistenza alle scorie, stabilità agli shock termici ed elevata conduttività termica. Il loro contenuto di carbonio è compreso tra il 10% e il 20%.
Materiali refrattari per pareti laterali di forni elettrici ad altissima potenza
Le pareti laterali dei forni elettrici ad altissima potenza (forni UHP) sono per lo più realizzate con mattoni MgO-C, mentre i punti caldi e le aree di scoria sono realizzati con mattoni MgO-C dalle prestazioni eccellenti (come i mattoni MgO-C a matrice di carbonio integrale). Ne migliorano significativamente la durata utile.
Sebbene il carico sulle pareti del forno sia stato ridotto grazie ai miglioramenti nei metodi di funzionamento dei forni elettrici, è ancora difficile per i materiali refrattari prolungare la durata dei punti caldi quando si opera in condizioni di fusione UHP. Pertanto, è stata sviluppata e applicata la tecnologia di raffreddamento ad acqua. Per i forni elettrici che utilizzano la colata EBT, l'area di raffreddamento ad acqua raggiunge il 70%, riducendo così notevolmente l'uso di materiali refrattari. La moderna tecnologia di raffreddamento ad acqua richiede mattoni in MgO-C con buona conduttività termica. Per costruire le pareti laterali del forno elettrico vengono utilizzati asfalto, mattoni in magnesia legati con resina e mattoni in MgO-C (contenuto di carbonio 5%-25%). In condizioni di ossidazione severe, vengono aggiunti antiossidanti.
Per le aree hotspot più gravemente danneggiate dalle reazioni redox, per la costruzione vengono utilizzati mattoni MgO-C con magnesite fusa cristallina di grandi dimensioni come materia prima, un contenuto di carbonio superiore al 20% e una matrice interamente in carbonio.
L'ultimo sviluppo dei mattoni MgO-C per forni elettrici UHP consiste nell'utilizzare la cottura ad alta temperatura e la successiva impregnazione con asfalto per produrre i cosiddetti mattoni MgO-C impregnati di asfalto cotto. Come si può vedere dalla Tabella 2, rispetto ai mattoni non impregnati, il contenuto di carbonio residuo dei mattoni MgO-C cotti dopo l'impregnazione con asfalto e la ricarbonizzazione aumenta di circa l'1%, la porosità diminuisce dell'1% e la resistenza alla flessione ad alta temperatura e alla pressione sono migliorate. La resistenza è stata notevolmente migliorata, quindi ha un'elevata durabilità.
Materiali refrattari al magnesio per pareti laterali di forni elettrici
I rivestimenti dei forni elettrici si dividono in alcalini e acidi. I primi utilizzano materiali refrattari alcalini (come magnesia e materiali refrattari MgO-CaO) come rivestimento del forno, mentre i secondi utilizzano mattoni di silice, sabbia di quarzo, fango bianco, ecc.
Nota: per i materiali di rivestimento dei forni, i forni elettrici alcalini utilizzano materiali refrattari alcalini, mentre i forni elettrici acidi utilizzano materiali refrattari acidi.
Data di pubblicazione: 12-10-2023