I getti refrattari a basso contenuto di cemento vengono confrontati con i tradizionali getti refrattari in cemento alluminato. La quantità di cemento aggiunta nei getti refrattari in cemento alluminato tradizionali è solitamente del 12-20%, mentre la quantità di acqua aggiunta è generalmente del 9-13%. A causa dell'elevata quantità di acqua aggiunta, il corpo del getto presenta molti pori, non è denso e ha una bassa resistenza; a causa dell'elevata quantità di cemento aggiunto, sebbene si possano ottenere resistenze più elevate a temperatura normale e a bassa temperatura, la resistenza diminuisce a causa della trasformazione cristallina dell'alluminato di calcio a temperature medie. Ovviamente, il CaO introdotto reagisce con SiO₂ e Al₂O₂ nel getto per generare alcune sostanze a basso punto di fusione, con conseguente deterioramento delle proprietà del materiale alle alte temperature.
Utilizzando la tecnologia delle polveri ultrafini, additivi ad alta efficienza e una gradazione scientifica delle particelle, il contenuto di cemento del colabile si riduce a meno dell'8% e il contenuto d'acqua a ≤7%, consentendo di preparare e portare a termine un colabile refrattario a basso contenuto di cemento. Il contenuto di CaO è ≤2,5% e i suoi indicatori di prestazione generalmente superano quelli dei colabili refrattari a base di cemento alluminato. Questo tipo di colabile refrattario ha una buona tissotropia, ovvero il materiale miscelato assume una certa forma e inizia a fluire con una piccola forza esterna. Quando la forza esterna viene rimossa, mantiene la forma ottenuta. Pertanto, è anche chiamato colabile refrattario tissotropico. Il colabile refrattario autofluente è anche chiamato colabile refrattario tissotropico. Appartiene a questa categoria. Il significato preciso di colabile refrattario a basso contenuto di cemento non è stato ancora definito. L'American Society for Testing and Materials (ASTM) definisce e classifica i materiali refrattari in base al loro contenuto di CaO.
Densità e alta resistenza sono le caratteristiche principali dei calcestruzzi refrattari a basso contenuto di cemento. Questo è un vantaggio per migliorare la durata e le prestazioni del prodotto, ma può anche causare problemi di cottura prima dell'uso, ovvero, se non si presta attenzione durante la cottura, si può facilmente verificare la fuoriuscita di acqua. Il fenomeno dello scoppio del corpo può richiedere almeno una nuova colata o, nei casi più gravi, può mettere a repentaglio la sicurezza personale dei lavoratori circostanti. Pertanto, diversi paesi hanno condotto studi sulla cottura dei calcestruzzi refrattari a basso contenuto di cemento. Le principali misure tecniche sono: la formulazione di curve di cottura ragionevoli e l'introduzione di eccellenti agenti antideflagranti, ecc., che consentono di eliminare l'acqua dai calcestruzzi refrattari senza causare altri effetti collaterali.
La tecnologia delle polveri ultrafini è la tecnologia chiave per i materiali refrattari colabili a basso contenuto di cemento (attualmente la maggior parte delle polveri ultrafini utilizzate in ceramica e materiali refrattari ha dimensioni comprese tra 0,1 e 10 µm e funzionano principalmente come acceleratori di dispersione e densificatori strutturali). La prima rende le particelle di cemento altamente disperse senza flocculazione, mentre la seconda riempie completamente i micropori nel corpo di colata e ne migliora la resistenza.
I tipi di polveri ultrafini attualmente più comunemente utilizzati includono SiO2, α-Al2O3, Cr2O3, ecc. L'area superficiale specifica della micropolvere di SiO2 è di circa 20 m2/g e la sua dimensione delle particelle è circa 1/100 della dimensione delle particelle di cemento, quindi ha buone proprietà di riempimento. Inoltre, le micropolveri di SiO2, Al2O3, Cr2O3, ecc. possono anche formare particelle colloidali in acqua. In presenza di un disperdente, si forma un doppio strato elettrico sovrapposto sulla superficie delle particelle per generare una repulsione elettrostatica, che supera la forza di van der Waals tra le particelle e riduce l'energia di interfaccia. Ciò impedisce l'adsorbimento e la flocculazione tra le particelle; allo stesso tempo, il disperdente viene adsorbito attorno alle particelle per formare uno strato di solvente, che aumenta anche la fluidità del colabile. Questo è anche uno dei meccanismi della polvere ultrafine, ovvero l'aggiunta di polvere ultrafine e di disperdenti appropriati può ridurre il consumo di acqua dei materiali refrattari e migliorarne la fluidità.
La presa e l'indurimento dei calcestruzzi refrattari a basso contenuto di cemento sono il risultato dell'azione combinata di legame per idratazione e legame per coesione. L'idratazione e l'indurimento del cemento di alluminato di calcio sono principalmente dovuti all'idratazione delle fasi idrauliche CA e CA2 e al processo di crescita cristallina dei loro idrati, ovvero alla reazione con l'acqua per formare scaglie esagonali o aghiformi di CAH10, C2AH8 e prodotti di idratazione come cristalli cubici di C3AH6 e gel di Al2O3аq, che formano poi una struttura reticolare di condensazione-cristallizzazione interconnessa durante i processi di stagionatura e riscaldamento. L'agglomerazione e l'indurimento sono dovuti alla formazione di particelle colloidali da parte della polvere ultrafine di SiO2 attiva quando incontra l'acqua, e agli ioni lentamente dissociati dall'additivo aggiunto (ovvero la sostanza elettrolitica). Poiché le cariche superficiali dei due sono opposte, ovvero la superficie del colloide ha adsorbito controioni, causando il £2. Il potenziale diminuisce e si verifica la condensazione quando l'adsorbimento raggiunge il "punto isoelettrico". In altre parole, quando la repulsione elettrostatica sulla superficie delle particelle colloidali è inferiore alla sua attrazione, si verifica un legame coesivo con l'aiuto della forza di van der Waals. Dopo che il colabile refrattario miscelato con polvere di silice è condensato, i gruppi Si-OH formati sulla superficie di SiO₂ vengono essiccati e disidratati a ponte, formando una struttura reticolare silossanica (Si-O-Si), indurendo così. Nella struttura reticolare silossanica, i legami tra silicio e ossigeno non diminuiscono all'aumentare della temperatura, quindi anche la resistenza continua ad aumentare. Allo stesso tempo, ad alte temperature, la struttura reticolare di SiO₂ reagirà con l'Al₂O₂ in essa avvolto per formare mullite, che può migliorare la resistenza a medie e alte temperature.
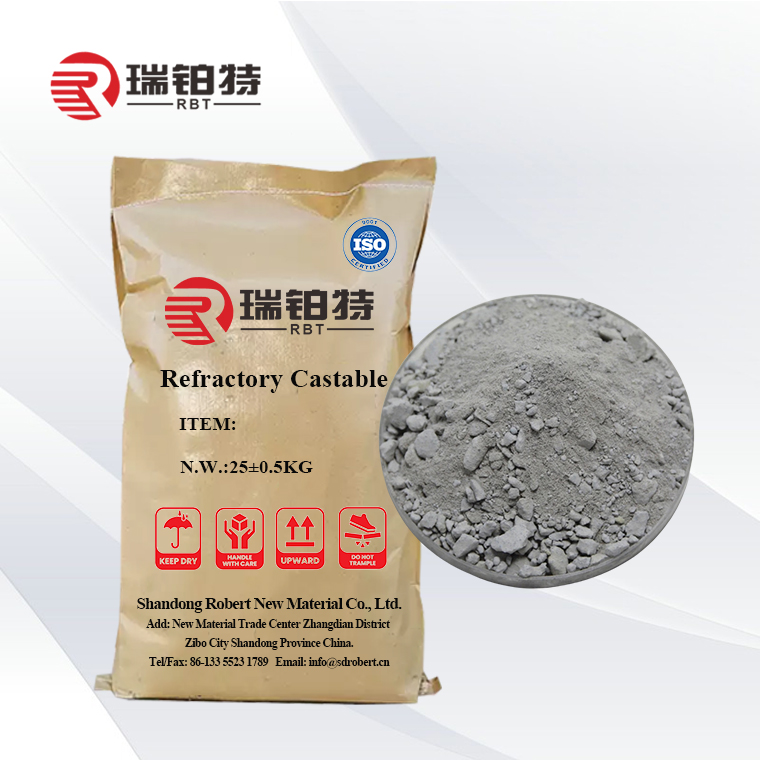
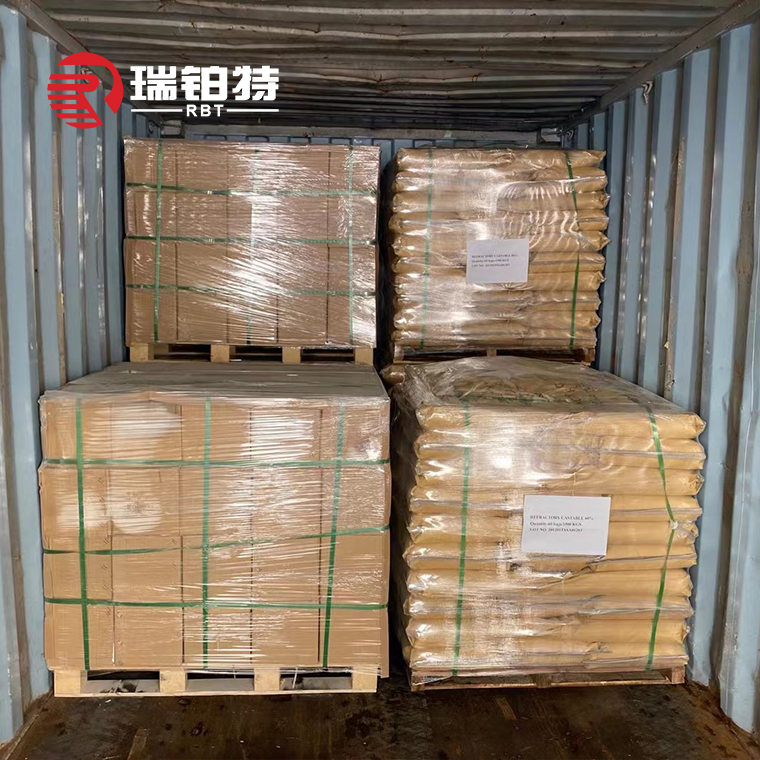
Data di pubblicazione: 28 febbraio 2024